How to manage moisture-sensitive components in PCBA processing
In the process of PCBA (printed circuit board assembly), the management of moisture-sensitive electronic components is crucial. Improper management of moisture-sensitive components will lead to welding defects, such as cold solder joints, bridging tin and insufficient tin, which will affect the quality and reliability of the product. The following will introduce the management methods of moisture-sensitive components in detail from the two aspects of storage and feeding.
Management methods of moisture-sensitive components in PCBA processing
Storage management
1. Moisture sensitivity level (MSL)
Each moisture-sensitive component has its own moisture sensitivity level (MSL). MSL clearly stipulates the maximum exposure time allowed for moisture-sensitive components and the use of feeding intervals. MSL classification is as follows:
- Class 1 – less than or equal to 30°C/85% RH, unlimited floor life
- Class 2 – less than or equal to 30°C/60% RH, one year floor life
- Class 2a – less than or equal to 30°C/60% RH, four weeks floor life
- Class 3 – less than or equal to 30°C/60% RH, 168 hours floor life
- Class 4 – less than or equal to 30°C/60% RH, 72 hours floor life
- Class 5 – less than or equal to 30°C/60% RH, 48 hours floor life
- Class 5a – less than or equal to 30°C/60% RH, 24 hours floor life
- Class 6 – less than or equal to 30°C/60% RH, 12 hours floor life (needs to be baked before use)
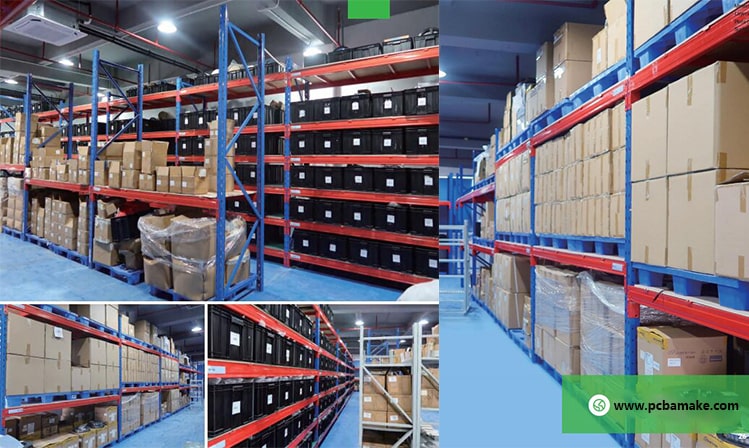
2. Storage in moisture-proof cabinets
Humidity-sensitive components should be stored in moisture-proof cabinets with specific functions. In order to ensure the stability of the storage environment, it is recommended to install a temperature and humidity alarm on the moisture-proof cabinet so that an alarm and manual intervention can be performed when the humidity exceeds the standard. The humidity in the moisture-proof cabinet should be maintained below 10% RH to ensure that the humidity-sensitive components are not affected by moisture.
3. Humidity label card management
Every time a humidity-sensitive component is taken out, the condition of its humidity label card must be checked, and the removal time and the return time of the remaining material must be recorded. The humidity label card can show whether the component has been damp during storage so that it can be baked if necessary.
Material management
1. Material collection and feeding
During the material collection and feeding process of humidity-sensitive components, the maximum exposure time specified by MSL must be strictly followed. Components that have not been used up within the exposure time must be stored again in the moisture-proof cabinet. If the exposure time of the humidity-sensitive component exceeds the specified time, it must be strictly baked before going online.
2. Baking treatment
Baking treatment is to completely remove moisture from moisture-sensitive components to avoid quality problems caused by moisture expansion during the welding process. The baking condition is usually 125°C, and the baking time depends on the component type and exposure time.
Moisture Sensitivity Level Determination Process
In order to ensure the quality of moisture-sensitive components, moisture sensitivity level (MSL) determination is required. The determination process is as follows:
1. Initial inspection: SAT test is performed on good ICs to confirm that there is no delamination.
2. Baking treatment: Bake the IC to completely remove moisture.
3. Humidification treatment: Humidification treatment is performed according to the MSL level.
4. Reflow test: IR-Reflow is performed 3 times (simulating IC loading, repair and disassembly, and reloading).
5. Final inspection: SAT inspection is performed to check whether there is delamination and IC function test.
If the component passes the above test, it means that its package meets the MSL level.
Record management
PCBA processing plants should formulate strict forms and require operators to register before each placement, inspection and feeding. These records help track the use of moisture-sensitive components and ensure the effectiveness of materials.
The management of moisture-sensitive components is a crucial part of PCBA processing and must be strictly controlled and managed. Through scientific storage, feeding and record management, welding defects can be effectively avoided and the quality and reliability of products can be improved. The management of moisture-sensitive components requires not only equipment support, but also strict implementation and meticulous operation by operators. Only in this way can the smooth progress of the PCBA processing process be ensured.
PCBAMake has an independent component warehouse, which stores and preserves various components according to different needs. Professional staff strictly store them according to storage conditions to ensure product quality. In addition, we also have a component warehouse in Hong Kong, where foreign imports are sent to Hong Kong as the first stop, saving customers a lot of import taxes and fees. At the same time, we can also help customers send goods from Hong Kong to the world, saving customers freight and import taxes and fees, and only charging a small amount of labor operation costs. And we can help customers store goods in Hong Kong, charge customers for storing goods according to our rental cost price, save customers international logistics expenses and still have a lot of space for storage.