Today we are going to discuss our quality control process. How do we ensure the quality of PCBA?
How Do We Ensure the Quality of PCBA?
We have many quality control steps to ensure our products meet the highest standards. Let's go through them one by one.
First of all, IQC Process. We check the incoming components before SMT assembly. According to the production needs, we will check the QTY, part number, specification, silkscreen marking of each component,to see if it match with the pads,and whether the component is coordinate with BOM.
QE team checks every component in the BOM to match with its pad in Gerber once order is released from customer. If any issues, we will feedback to customers and provide professional recommendations.
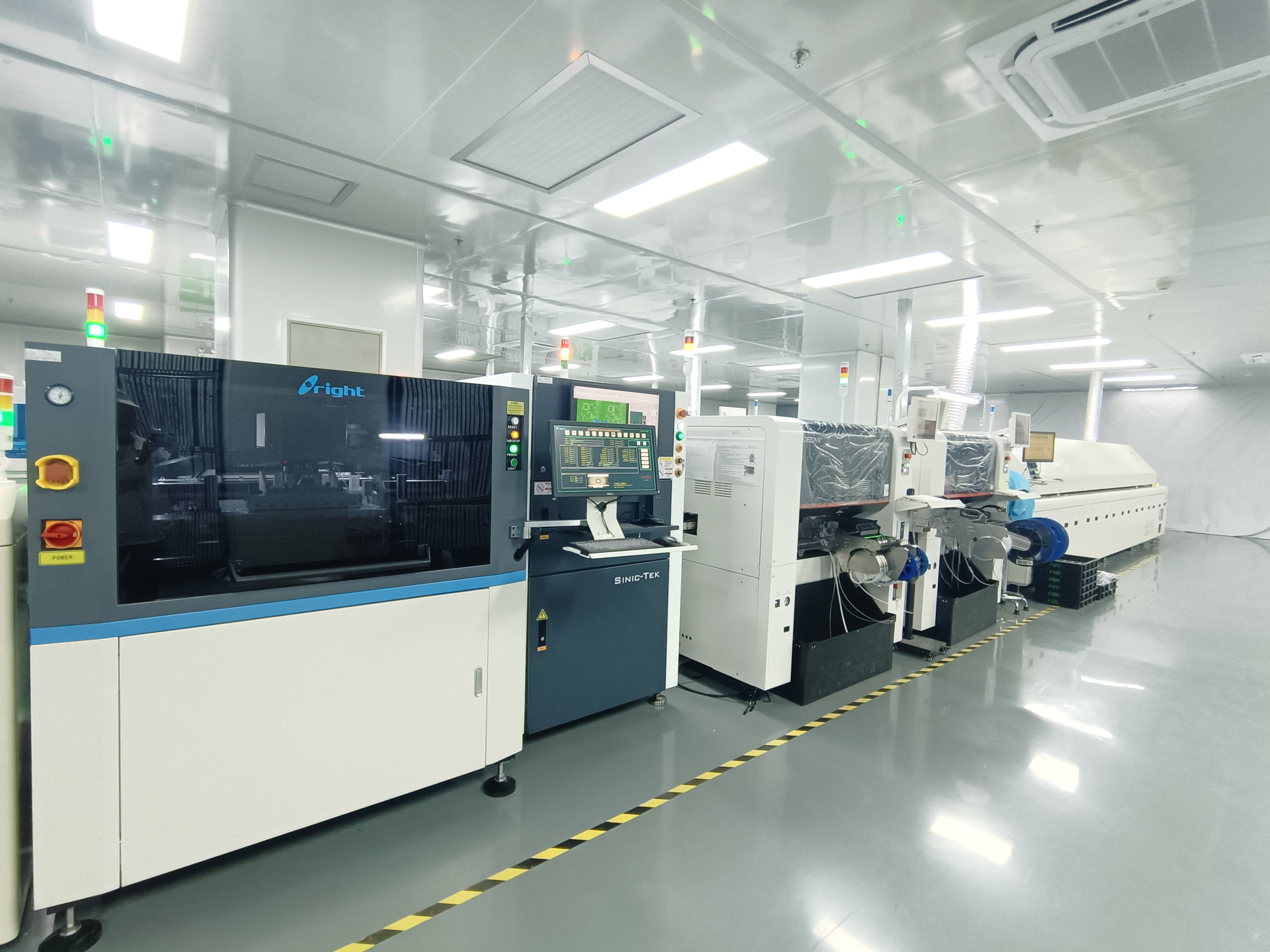
IQC is a critical process: whether components received coordinate with BOM, like quantity, part number, date code, parts appearance, ect.
In addition we have FAI inspection, AOI inspection, x-ray inspection, and visual inspection during the production process to ensure our quality, and we can also carry out functional testing according to the customer’s requirements.
All products here will be 100% tested rigorously before delivery.
Will PCBAMake be able to carry out programming and functional testing? What documents are required?
PCBAMake carry out programming and functional testing. The documents required for programming and functional testing vary from the project's requirements.
There are two programming methods.
One is programming before assembly, need HEX or BIN files and IC Part number.
The other one is programming after assembly, except for the above, please also provide the firmware file and upload instructions.
Regarding functional testing, we may need you to provide the testing process and the tools you may need for testing. We can also customize test jigs if needed.
Our engineers are professional and experienced. They are able to complete testing according to your requirements. Besides, welcome to our factory for guidance and testing directly.
What if the customers find any defects or problems after receiving the PCBA?
As we all know, PCBA production is demanding work, many details involved. If customers find any defects or quality issues, We will thoroughly analyze the problem and come up with the best solution to fix it. If the quality problem is a result of our mistake and the customer cannot repair the defective boards on their own, we may request that the customer return the defective boards for repair.
We guarantee every board is good and functional in your hands! PCBAMake values every customer and always pursue long-term cooperation.