PCBA processing solder joint failure
Electronic devices are now more and more, and many things are developing in the direction of intelligence. This requires more circuit boards to undertake the control system of these devices. The quality of PCBA processing determines the service life of the equipment.
The quality of the welding joint is the most important part of PCBA processing. The reliability of the quality of the welding joint determines the reliability and service life of PCBA products. Once the solder joints fail, the PCBA will be repaired or scrapped. The reliability of improving the welding joint is one of the processing goals of the PCBA electronic processing plant.
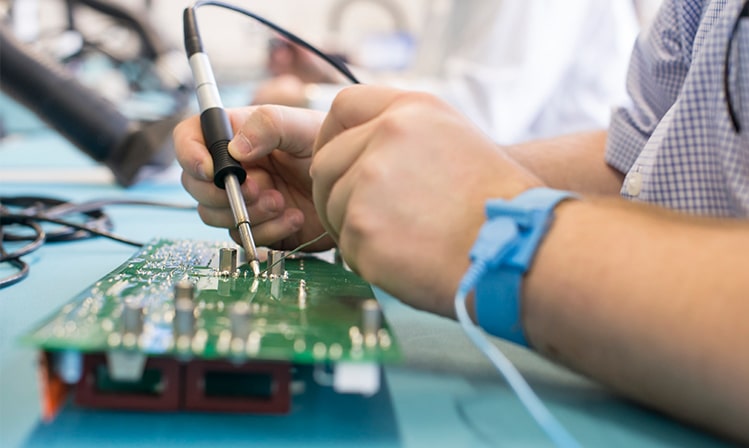
Common causes of PCBA processing welding defects.
Poor component pins: plating, pollution, oxidation or poor coexistence of pins, affect the quality and reliability of welding.
Poor PCB pads: The coating, pollution, oxidation or warning of the pads, cause poor or broken welding dots.
Weld quality defects: The composition of welds, impurities, or oxidation do not meet the standards, affecting the mechanics and electrical properties of the welded joints.
Welding quality defects: The welding, corrosion, or surface insulation resistance (SIR) of the welds is unqualified, resulting in virtual welding, cold welding or leakage of the welded joints.
Process parameter control defects: There are problems in process design, control or equipment, which causes the welding temperature, time, and speed of the parameters in improper, which affects the formation and stability of the welding joint.
Other auxiliary materials defects: the quality or use of auxiliary materials such as adhesives, cleaning agents, and improper use, causing the solder joints to be contaminated or damaged.
There are the following solutions to the failure of PCBA processing solder joints:
1. Check and improve the quality of component pins and PCB pads: Select qualified components and PCB to avoid using polluting or oxidative materials to ensure the cleaning and rectification of pins and pads.
2. Check and improve the quality of welded and welded: Select welded and solder that meets standards, avoid using expired or oxidized materials, and ensure freshness and applicability of welds and welds.
3. Check and improve the control of process parameters: According to the characteristics of components and PCB, determine reasonable process parameters, such as temperature, time, speed, etc. to ensure the accuracy and stability of the process parameters.
4. Check and improve the use of other auxiliary materials: Select the appropriate auxiliary materials such as adhesives, cleaning agents, and use it according to specifications to ensure the effectiveness and safety of the auxiliary materials.
If you want to know more, you can pay attention to Lingzhuo. If you need to learn more about PCB Prototype, SMT patch, PCBA service processing related technical knowledge, please leave a message to get it!