PCBAMake Solder Paste Storage and Operation Norms
In the SMT production line, quality is the top priority, and this production of defective rate of 60%-70% is generated in the soldering process, most of the reasons are related to the use of solder paste and improper storage.
PCBAMake adheres to the following norms during assembly process to ensure the quality of the solder as well as the product.
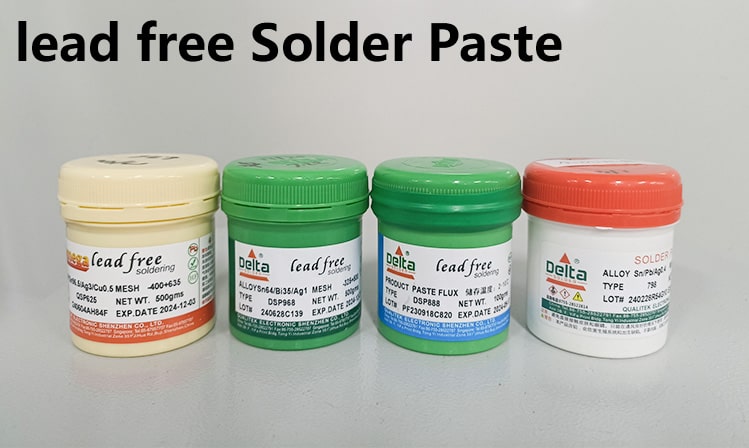
(1)Before the solder paste is stored in the warehouse, it needs tod be labeled with the date of purchase to distinguish different batches. We will control the use of solder paste cyde according to the SMT orders, since the inventory is generally controlled within 30 days. And solder paste storage should be placed separately according to different types, batch numbers, different manufacturers, solder paste should be stored in refrigeration after purchase and should follow the principle of first-in-first-out.
(2)The solder paste is stored in the refrigerator, which is equipped with a special thermometer, and its storage temperature shall be controlled within the range of 2-10°℃, and our PCBAMake staff will test the storage temperature every 12 hours and make a record.
(3)Take out of the refrigerator at least 4 hours prior to use and wait the solder paste to return to room temperature before opening the container to prevent condensation of water vapor and the formation of solder beads.
(4)After opening, we will use a mixer to make the ingredients in the solder paste uniform and reduce the viscosity of the paste.lead free
(5)Our staffs usually decide the thickness of solder paste according to the thickness of the stencil and the components on the PCB circuit board to ensure the printing quality. For example, there are stencil thickness specifications of O. tmm,0.12mm, 0.13mm, 0.15mm, 0.18mm, 0.2mm, etc. Usually, for a 0.12mm thick stencil, the thickness of the solder paste is usually controlled between 0.Imm-0.16mm.
(6)PCB board after printing solder paste should be posted in the shortest possible time to prevent fux paste and other solvents volatile. After printing falures, PCB bords should be required to be thoroughly deaned and dried with ultrasonic deaning equipment, in order to prevent the emergence of solder balls caused by residual solder paste after reflow soldering again.
(7)There is strict termperature control in our SMT PCBA production line. The optimal temperature for printing is 25C3C and the relative temperature should be 45%-65%. If the temperature is too high, the solder paste will easily absorb water vapor and produce solder beads during reflow soldering.
(8)After the solder paste printing machine, we will use SPi to carry out 10% inspection on the quality of the solder paste printing, it can effectively detect the printing volume, height, area, flatness and other defects of the solder paste, to ensure the quality of the printing and the final product.