PCB Assembly proofing process
PCBA prototyping, or prefabricated electronic printed circuit board assembly, is an indispensable part of modern electronic product manufacturing. For companies developing new products, the PCB assembly service prototyping process is a key step to verify the feasibility of their designs. This article will introduce the entire process of PCBA proofing in detail.
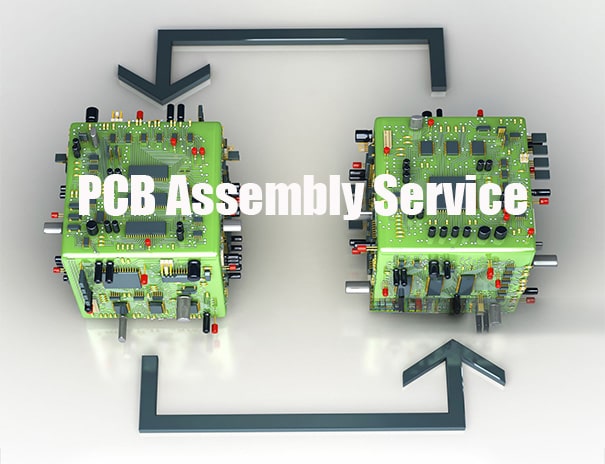
1. Clarify requirements and specifications
Before starting PCBA prototyping, you first need to clarify the customer's needs, including the functions, dimensions, interface types, component specifications, etc. of the required circuit board. In addition, the quantity of samples, delivery time, etc. need to be clarified. Making sure these details are clear will help the process go smoothly.
2. Schematic diagram and PCB design
According to the customer's needs, the schematic design is carried out, that is, the connection relationship between the components is determined. Subsequently, professional software is used for PCB (Printed Circuit Board) design to determine the layout and connection of components on the circuit board. This step requires special attention to details such as component packaging, wiring width, and spacing to ensure the performance and reliability of the circuit board.
3. Project review and modification
After completing the preliminary schematic and PCB design, an engineering review is required to check whether there are errors or unreasonable aspects in the design. This link is very critical, as it can effectively avoid problems in subsequent production. Based on the results of the engineering review, necessary modifications are made to the schematic and PCB design.
4. PCBA Prototyping and Processing
After the design is confirmed to be correct, enter the PCBA proofing and processing stage. This step includes board casting, welding, testing and other links. Boarding is to hand over the designed PCB to the factory for production; welding is to solder electronic components to the PCB; testing is to test the function and performance of the completed PCBA to ensure that it meets the requirements.
5. Sample acceptance and feedback
After receiving the sample, the customer needs to accept the PCBA to check whether its appearance, function and performance meet expectations. If there are any problems, please provide timely feedback to the supplier for improvement and optimization. This step is an important step in ensuring the rights and interests of both parties.
6. Small batch production and testing
After passing the sample acceptance, small batch production can be carried out to further verify the stability and reliability of the production process. At the same time, the produced PCBA can also be tested more deeply to provide data support for subsequent mass production.
The PCBA prototyping process involves multiple links, and each step requires careful consideration and strict control. Only in this way can the quality and reliability of the final product be ensured and meet customer expectations.